By using manufacturing-specific software solutions and intelligent operational strategies, you can gain a comprehensive view of your inventory, regardless of the number of locations.
Effective inventory management ensures that you always have the right amount of inventory at the right time, reducing waste and improving cash flow. By centralising control and utilising forecasting tools, you can better predict customer demands and allocate resources where they're needed most. This approach not only streamlines operations but also enhances customer satisfaction.
Incorporating best practices in your stock management processes improves accuracy and efficiency. For example, digital inventory systems can automate many tasks, reducing human error and freeing up time for strategic decisions. These systems also offer seamless integration with other business processes, creating a more cohesive workflow.
Key takeaways
- Efficient inventory management systems are key for handling stock across multiple locations.
- Accurate forecasting and centralised control help optimise stock levels.
- Digital systems and automation enhance overall efficiency and customer satisfaction.
Inventory management systems and software
Effective inventory management is crucial for handling multiple locations in manufacturing. Utilising robust warehousing management software, integrating systems across your sites and leveraging real-time tracking can greatly enhance accuracy and efficiency.
Choosing the right inventory management software
Selecting the right inventory management software is essential. Key features to look for include:
- scalability: the software should grow with your business
- ease of use: choose a user-friendly interface
- integration capabilities: Ensure it works well with your existing systems
- support and training: good customer support and training resources are vital.
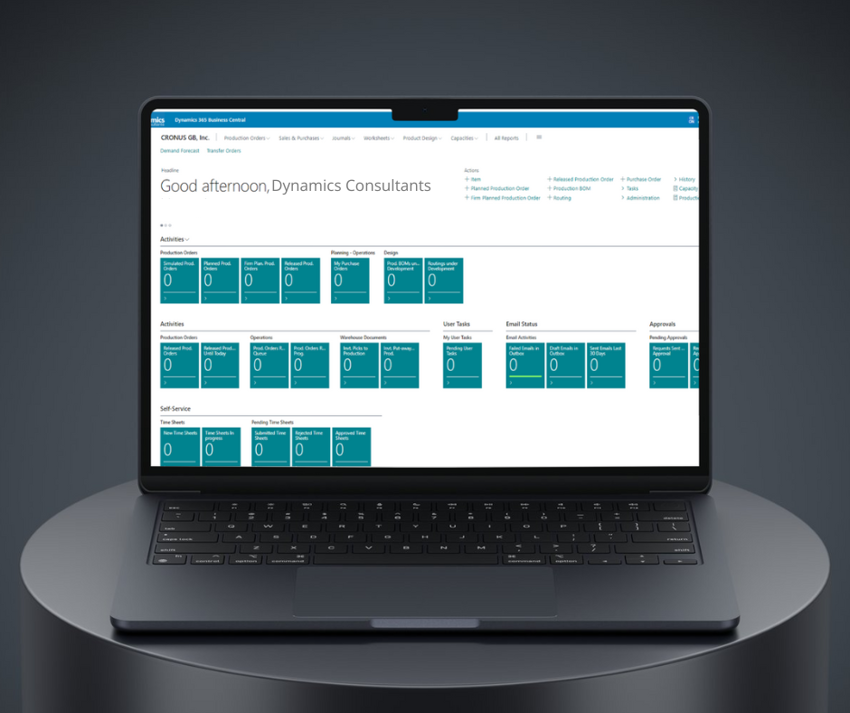
Using reliable inventory management software can streamline operations and improve accuracy. Microsoft Dynamics 365 is a robust solution tailored for manufacturing needs, with specific functions for stock and warehouse management.
Integrating systems across multiple locations
Integrating inventory management systems across multiple locations is critical. This ensures seamless information flow and consistency. When integrating, consider:
- unified data: centralise data into a single version of the truth to access real-time updates
- standard processes: implement standard operating procedures across all locations
- communication tools: Use tools that facilitate communication between sites
Adopting integrated systems helps synchronise inventory across warehouses, reducing discrepancies and improving overall efficiency. This also aids in demand forecasting and stock replenishment.
Real-time tracking and electronic systems
Real-time tracking and electronic systems are key components of modern inventory management. Advantages include:
- instant updates: real-time data provides instant inventory status
- reduced errors: electronic tracking systems minimise manual errors
- improved accuracy: real-time tracking ensures inventory accuracy
Implementing real-time tracking in Dynamics 365 can significantly boost operational efficiency. Technologies like RFID, barcoding and IoT devices provide accurate, up-to-date inventory details, helping you make informed decisions swiftly.
Optimisation of stock levels
To maintain efficient stock management for manufacturing across multiple locations, you need to focus on accurate demand forecasting, reducing excess inventory and managing inventory costs.
Demand forecasting and safety stock
Accurate demand forecasting is critical to optimise stock levels. It involves analysing historical data, market trends and sales projections to predict future demand. Using advanced forecasting tools can help you make more precise predictions.
Safety stock is the buffer inventory kept to prevent stockouts due to unexpected demand spikes or supply chain disruptions. By carefully calculating safety stock, you can balance the need for readiness against the costs of holding extra inventory.
Reducing excess inventory
Excess inventory ties up capital and storage space, which can increase holding costs. To reduce excess inventory, start with a thorough analysis of your stock turnover rates. Items that move slowly need to be flagged for reduction.
Implementing a point-of-sale (POS) system or inventory management software helps track inventory levels in real-time. This technology enables you to identify slow-moving items and decide whether to discount them, return them to suppliers or even discontinue them.
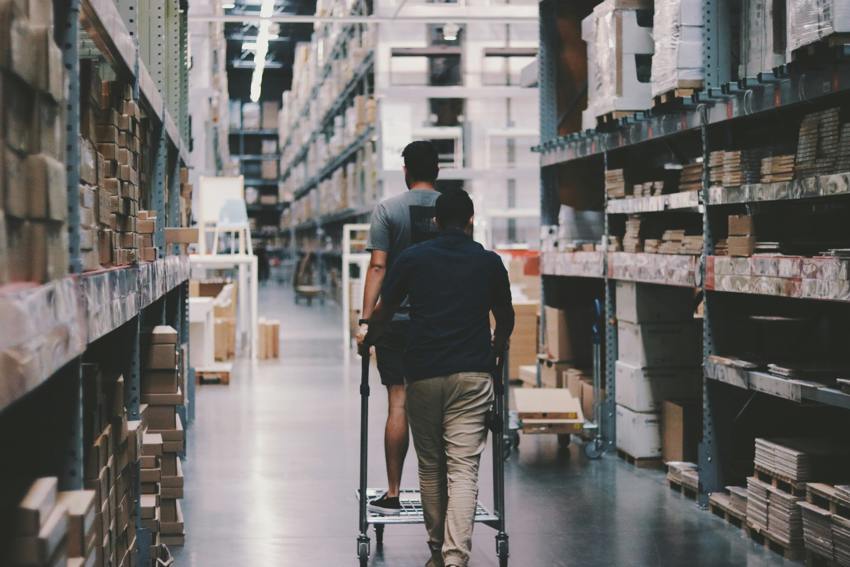
Inventory valuation and cost management
Correct inventory valuation ensures accurate financial reporting and helps in cost management. Methods like FIFO (first-in, first-out) or LIFO (last-in, first-out) impact your cost of goods sold and profitability.
It's essential to consider the cost of inventory holding, which includes storage, insurance and taxes. Reducing these costs increases your overall efficiency. Monitoring and managing these expenses allows for better budgeting and improved financial health.
By maintaining optimal stock levels, you can strike a balance between meeting customer demand and controlling inventory costs.
Operational strategies for effective stock management
Effective stock management involves using various strategies to streamline operations, reduce costs and ensure that products are available when needed. This includes practices such as continuous improvement, developing detailed replenishment plans and implementing stock rotation and auditing techniques.
Continuous improvement and lean management
Continuous improvement and lean management focus on constantly refining processes to eliminate waste and increase efficiency.
Lean management principles involve identifying and removing non-value-added activities in your supply chain. This leads to reduced lead times, more accurate inventory levels and better utilisation of resources. Implementing these strategies helps you maintain competitive advantage by enhancing your overall operational efficiency.
Developing a stock replenishment plan
A well-developed stock replenishment plan ensures that you have the right products in the right quantities at the right time. Begin by setting your minimum stock levels and reorder points based on sales data and lead times from suppliers.
Incorporate methods like just-in-time and vendor-managed inventory to streamline your supply chain. These approaches reduce the need for large stockpiles and help prevent stockouts.
Additionally, using automatic replenishment systems can dynamically adjust your inventory based on current demand, ensuring you always have optimal stock levels. This strategic planning helps reduce excess inventory costs and improves service levels.
Stock rotation and auditing techniques
Stock rotation and auditing techniques are vital for maintaining inventory accuracy and freshness. Use the first-in, first-out method to ensure older stock is used or sold before newer stock, reducing waste and obsolescence.
Regular physical inventory counts and cycle counting assist in verifying stock levels and catching discrepancies early. Implementing these periodic checks ensures your inventory records are accurate and reliable.
Utilise technology like barcoding systems and RFID for real-time tracking of inventory. These tools help manage stock rotation effectively and enhance the accuracy of your physical inventory counts.
By employing these techniques, you can maintain effective stock control and minimise losses.
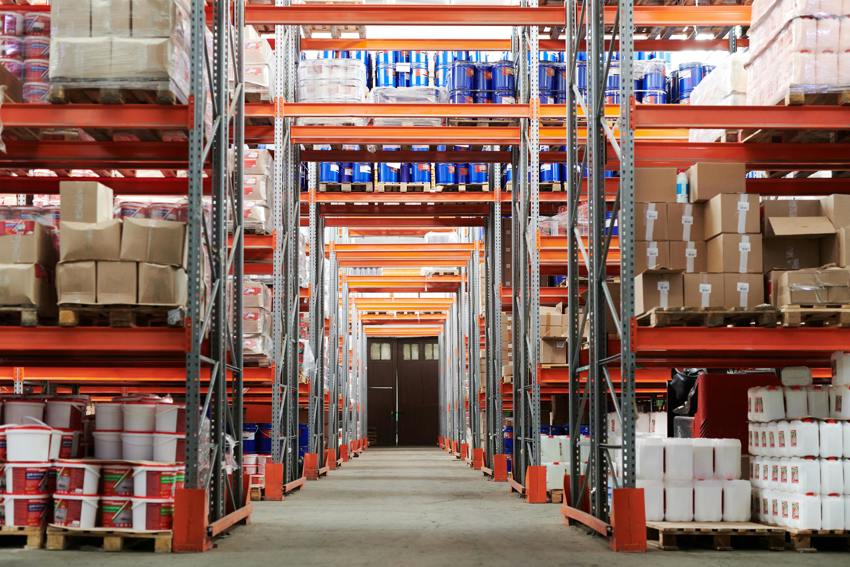
Frequently asked questions
This section covers key points on effectively managing inventory across multiple manufacturing facilities, recommended industry practices and the role of technology in streamlining inventory control.
How can I effectively manage inventory across multiple manufacturing facilities?
To manage inventory effectively across various facilities, you need a centralised system that updates in real-time, like Dynamics 365 Business Central. This ensures you always know your stock levels at each location. Implementing a robust inventory management software can help keep track of movements and reduce discrepancies.
What are the top industry-recommended practices for streamlining inventory control?
Top practices include regular audits, automated reordering and using just-in-time (JIT) inventory techniques. You should also embrace data analytics to predict demand accurately and adjust stock levels accordingly.
Image source: created by Rebellion
Which inventory allocation rules can enhance manufacturing efficiency?
Effective allocation rules focus on prioritising high-demand items and ensuring that stock is distributed where it is needed most. Utilise first-in, first-out (FIFO) principles to prevent inventory from becoming obsolete.
In what ways can technology facilitate more precise inventory management in manufacturing?
Technology offers various tools for precise inventory management. For instance, multi-location inventory management systems allow you to manage stock across numerous sites efficiently. Barcoding, RFID and IoT sensors also provide real-time tracking and minimise human errors.
How should a small manufacturing enterprise approach inventory management for optimal results?
Small enterprises should start with cost-effective inventory management solutions, such as simple software or even Excel spreadsheets. Eventually, as your business grows, transition to more sophisticated systems. Focus on balancing inventory levels to avoid overstocking and stockouts.
What considerations are critical when selecting a manufacturing inventory management system?
When choosing an inventory management system, consider scalability, ease of use and integration capabilities with your existing tools. It's also essential the system provides real-time updates and analytics to make informed decisions. Finally, ensure it supports multiple locations if you are managing several facilities.
Jesse Lawrence
Jesse is our marketing manager, keeping an eye on the latest news in the market as well as having worked on the GDPR legislation.