Improving your manufacturing efficiency is essential for meeting customer demands and maintaining high standards for quality products. Efficient manufacturing is not just about speeding up production; it's about producing quality products while minimising waste and reducing costs.
By integrating advanced tools and systems, you can streamline your operations and maintain consistency throughout your manufacturing process. This not only ensures faster turnaround times but also keeps your production costs in check. It's important to adopt strategies that align with your specific goals and continually seek ways to innovate and improve.
Establishing a focus on continuous improvement will position your business for long-term success. By embracing a proactive mindset, you'll be better equipped to adapt to changing market conditions and customer needs. Building a culture of innovation and efficiency enables your organisation to thrive.
Key takeaways
- Accurately measure your current manufacturing efficiency.
- Leverage technology for improved operational efficiency.
- Continuously seek improvement to meet evolving customer demands.
Understanding manufacturing efficiency
Manufacturing efficiency refers to how effectively a manufacturing operation converts inputs into outputs while minimising waste and costs. This involves strategic planning and optimising different components of the production process to maximise results.
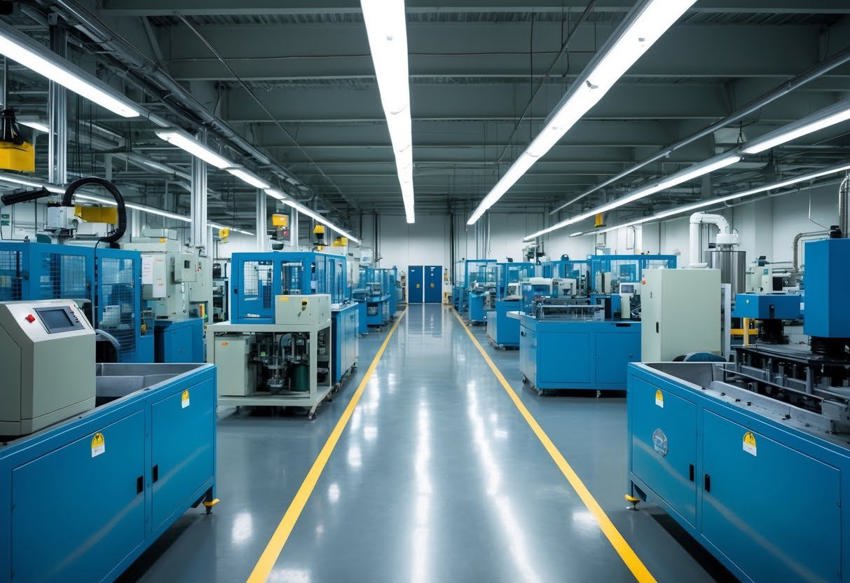
Key definitions and concepts
Manufacturing efficiency is the ability of a production process to meet high output standards with minimal costs and wasted resources. To increase efficiency, businesses need to focus on elements like resource allocation, equipment utilisation and workflow management.
Understanding these fundamentals helps you set realistic improvement goals and measure them effectively. One key comparison is measuring your standard output (your output goal), against your actual output (what you achieve). By frequently comparing the two, you get insights into performance and areas needing enhancement. Efficient manufacturing means smoother operations and cost reductions, making your business more competitive.
Assessing your current manufacturing processes
Evaluating your current production process helps you identify inefficiencies, which is the perfect place to start. Start by measuring actual output against the standard output to gauge performance. This can be done through metrics like production costs, quality rates and time efficiency.
Data collection across your entire manufacturing process helps you spot bottlenecks and areas where resources are underutilised. Monitoring systems and your back-office ERP solution can offer real-time insights into production processes, helping you adapt swiftly to changes.
Involving your team in assessments ensures that any changes you make are effective and sustainable. Employees offer valuable insights into daily operations and can help implement improvements that align with both immediate and long-term objectives. Engaging them helps create a more efficient workflow, reducing waste and increasing productivity.
The foundations of enhanced manufacturing efficiency
Improving manufacturing efficiency involves key principles that directly affect productivity and quality. Lean manufacturing, quality standards and preventive maintenance are pivotal in creating an optimised production process.
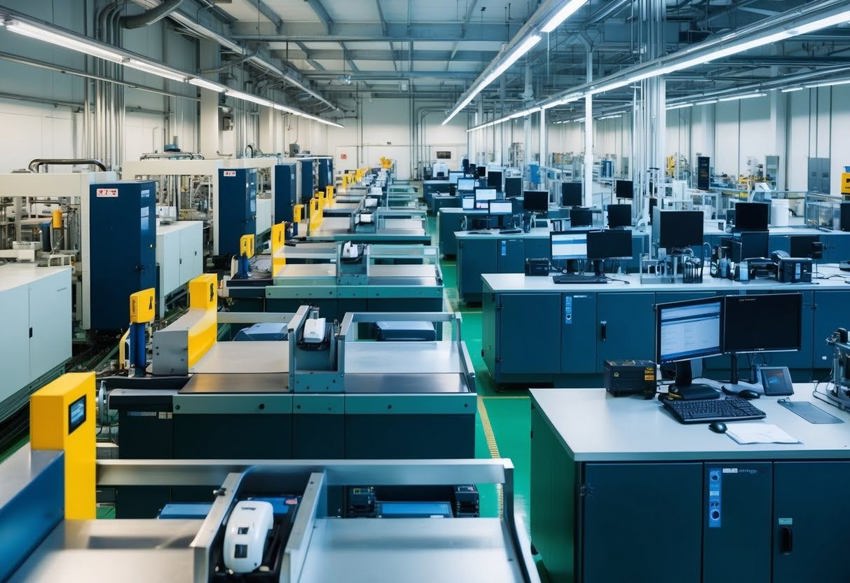
Lean manufacturing principles
Lean manufacturing focuses on eliminating waste and optimising processes. It can incorporate techniques like just-in-time (JIT), which ensures materials are only ordered and received when needed. This minimises inventory costs and reduces waste.
Incorporate value stream mapping to analyse and improve the flow of materials and information on production lines. By understanding each step in your process, you can identify areas to improve.
Continuous improvement encourages ongoing, incremental enhancements in efficiency. This approach demands regular assessment and adaptation, creating an environment where employees constantly work to advance processes at every level.
Quality standards and controls
Adhering to strict quality standards ensures your products meet customer expectations. Implementing robust quality control measures helps maintain consistency across production lines.
Standards such as ISO 9001 provide frameworks for creating a quality management system. These standards enhance customer satisfaction through established policies and procedures. Regular audits and training can also help ensure your team complies with required quality standards.
Focusing on quality early in the production process reduces defects and rework, saving you time and resources. This proactive approach means you can address any potential issues before they become larger problems.
Preventative maintenance strategies
Regular maintenance is vital for preventing equipment breakdowns, ensuring your production runs smoothly. Preventive maintenance involves scheduled inspections and servicing to avoid unexpected failures.
Use data-driven maintenance practices, incorporating predictive analytics to assess equipment health. By recognising patterns, you can anticipate issues before they arise, reducing downtime and repair costs.
Effective preventive maintenance boosts overall equipment effectiveness by increasing availability and performance. Implementing computerised maintenance management systems can further support scheduling and tracking your maintenance activities, ensuring nothing is overlooked.
Measuring manufacturing efficiency
Understanding how to measure manufacturing efficiency is essential for any business looking to maximise productivity and reduce costs. Devising key performance indicators helps you calculate and measure your business' efficiency.
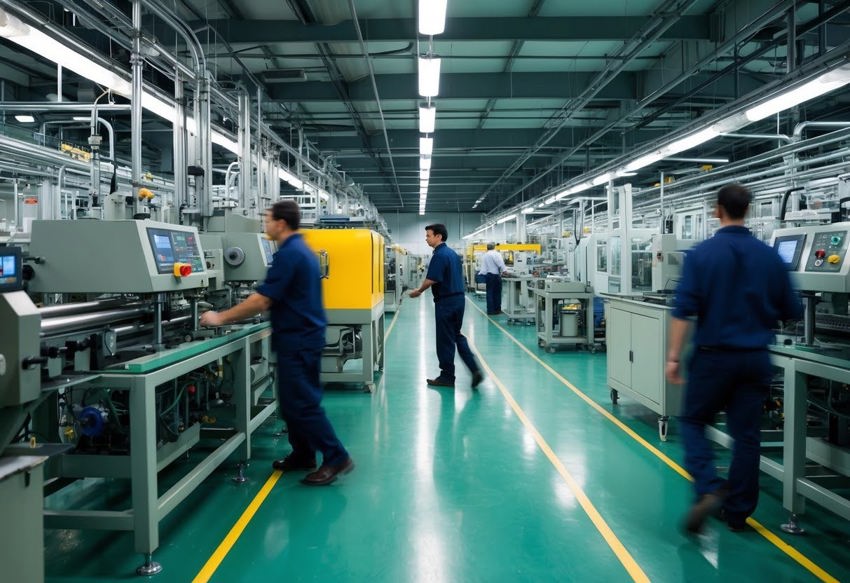
The role of key performance indicators
Key performance indicators (KPIs) play a key role in measuring manufacturing efficiency. They help you assess aspects like production capacity and operational efficiency. Common KPIs include overall equipment effectiveness (OEE), which considers availability, performance and quality.
Using KPIs, you can pinpoint areas for improvement. For instance, monitoring equipment downtime can highlight maintenance needs. By tracking yield rates, you ensure that less waste is produced.
Regularly reviewing these indicators allows you to adjust your processes and make data-driven decisions. Consistently evaluating KPIs keeps your operations aligned with strategic goals, ultimately enhancing productivity and reducing waste.
Calculating manufacturing efficiency formula
The manufacturing efficiency formula is straightforward yet powerful. It helps you understand how well your production processes convert resources into finished goods. The formula is:
Manufacturing efficiency = (actual output / standard output) * 100
This formula allows you to evaluate efficiency over time, noticing where improvements occur or where additional resources are required. Calculating efficiency involves comparing the actual output against an ideal or standard output.
By applying this formula, you get a clear picture of how effectively your resources are utilised. It helps you identify areas where improvements can be made, ensuring that your manufacturing process remains competitive and profitable. This approach is essential for maintaining a high standard of operational efficiency.
Technological advancements and manufacturing efficiency
Taking advantage of advanced technologies can significantly boost your manufacturing efficiency. By adopting smart factory solutions and using machine learning and AI, you can optimise operations, enhance productivity and reduce waste. These innovations enable real-time monitoring and refined processes, ensuring your factory operates at peak performance.
Implementing smart factory solutions
Smart factory solutions integrate advanced technologies like cloud manufacturing software and internet of things (IoT) devices to streamline your operations. This approach connects different facets of your manufacturing process, allowing for seamless data flow and improved efficiency.
One key component is real-time monitoring, which provides immediate insights into your production lines. By receiving instant feedback, you can swiftly address issues, reduce downtime and improve overall efficiency. Automation tools within these solutions can manage repetitive tasks, freeing up human resources for more complex roles. These functionalities are available in systems like Dynamics 365, which offers a single pane of glass through which you can see up-to-the-minute information on your business performance.
Smart energy solutions can also allow for better energy management. By monitoring usage in real-time, you can identify energy-saving opportunities and implement changes that reduce costs while maintaining productivity levels.
The impact of machine learning and AI
Machine learning and artificial intelligence (AI) play pivotal roles in refining manufacturing processes. These technologies analyse data patterns, predict potential issues and suggest improvements, making your operations more agile and responsive.
AI-driven analytics offer precise, data-backed decision-making tools, enhancing inventory management and demand forecasting. This predictive capability reduces overproduction and minimises waste, aligning your output more closely with market demands.
Furthermore, factory automation enhanced by machine learning improves quality control. By automatically detecting defects or anomalies, AI systems help maintain high standards without extensive human intervention. These advancements ensure your products meet quality benchmarks consistently, resulting in better customer satisfaction and loyalty.
Strategies for continuous improvement
Continuous improvement in manufacturing focuses on increasing efficiency and reducing waste. By managing resources better and engaging employees, you can create a more effective and sustainable work environment that benefits both your bottom line and the planet.
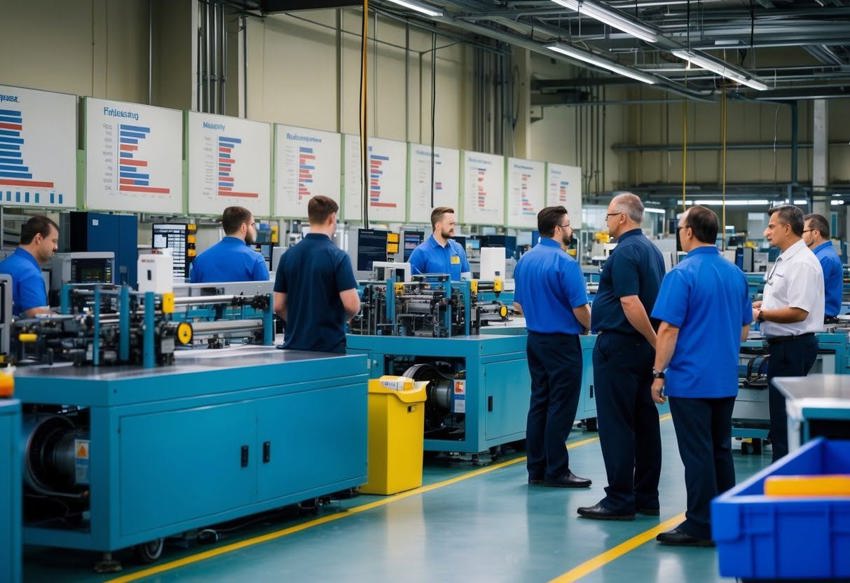
Resource management and waste reduction
Effective resource management is key to improving manufacturing efficiency. By closely analysing resource allocation, you can identify areas of excessive material waste and work to minimise it. Implementing lean manufacturing methods helps in creating more value with fewer resources. Techniques like just-in-time inventory can lower the environmental impact by reducing excess material stock.
Tracking and analysing data gives insights into areas where materials are wasted. With the help of various tools and processes, you can create plans for managing this waste effectively. Adopting sustainable practices not only improves the efficiency of production but also contributes to better environmental outcomes. This approach aims to cut down unnecessary usage and costs, resulting in a more streamlined operation.
Employee engagement and skill development
Involving employees in continuous improvement initiatives enhances their engagement and satisfaction. Providing opportunities for skill development empowers workers to contribute more effectively to the production process. When employees understand their role in improving efficiency, they are more likely to be motivated to participate actively.
Training programmes focused on skill enhancement make your workforce more versatile and capable of adopting new techniques. This can lead to innovations in procedures and an overall boost in productivity. Engaged and skilled employees become key assets, driving forward the goals of continuous improvement. Encouraging a culture of open communication and feedback ensures that suggestions for better practices are heard and implemented.
Frequently asked questions
Understanding manufacturing efficiency helps you improve productivity and competitiveness. This section addresses common questions about measuring and enhancing efficiency, as well as strategies and metrics.
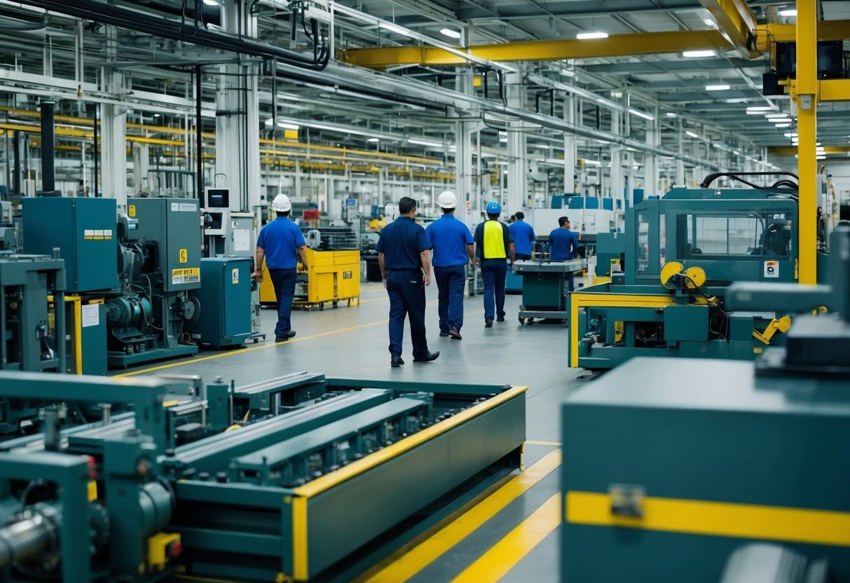
Can you detail some metrics that show enhanced production proficiency?
A drop in waste levels, increased output per hour and less downtime indicate an improvement. Keeping track of these metrics helps you spot where production processes are becoming more efficient.
What proven strategies exist for optimising efficiency within manufacturing systems?
Efficiency can be boosted by streamlining workflows, proactive equipment maintenance and adopting energy-saving techniques. Implementing lean manufacturing principles and continuous improvement methodologies are also effective strategies.
How is improved production efficiency quantified in practical scenarios?
Practical improvements can be seen in reduced lead times and cost savings. Enhanced efficiency often results in quicker order fulfilment and reduced operational expenses, showcasing tangible benefits.
What are the key elements that define manufacturing efficiency within an industrial context?
Key elements include the ratio of input to output, resource utilisation and production efficiency. Efficient use of materials, time and energy within your processes defines overall manufacturing efficiency.
Jesse Lawrence
Jesse is our marketing manager, keeping an eye on the latest news in the market as well as having worked on the GDPR legislation.