As manufacturing technologies have evolved, they have transformed processes and introduced new opportunities for growth. Advanced digital technology is also playing a crucial role in MRP, enabling more precise data collection and analysis. This means better decision-making capabilities for your business, leading to improved performance.
Adopting an MRP system can present certain challenges, which you need to consider. It's important to understand these aspects to make the transition as smooth as possible and maximise the benefits.
Key takeaways
- MRP enhances efficiency and productivity in manufacturing.
- Advanced digital technologies play a key role in modern MRP systems.
- Understanding challenges ensures a smoother MRP adoption.
Evolution of manufacturing technologies
The journey from steam power to advanced manufacturing technologies showcases significant advancements over time. Key industry 4.0 innovations such as cyber-physical systems and digital transformation have led to the development of smart factories, enhancing the efficiency and precision of production processes.

From steam to cyber-physical systems
In the 20th century, steam power revolutionised manufacturing by enabling mass production. Factories no longer relied solely on manual labour, which increased output and efficiency. Over time, this evolved into more sophisticated systems driven by electricity and automated machinery, paving the way for modernisation.
Today, the focus is on cyber-physical systems. These integrate computing, networking and physical processes, enabling smarter production environments. Cyber-physical systems contribute to the creation of smart factories, where machines communicate with each other and make autonomous decisions. This integration between machinery, devices and back-office systems enhances efficiency, reduces errors and allows for real-time adjustments in production.
Impact of digital transformation
Digital transformation has significantly impacted manufacturing, introducing enhanced telecommunications and interconnected systems. This shift allows for real-time data exchange between devices and improving coordination within the production line.
Advanced telecommunications allow for more efficient collaboration, streamlining decision-making processes. In these smart factories, you benefit from more tailored and efficient production strategies. Digital technologies enable predictive maintenance, minimising downtime and extending equipment lifespan. By embracing these innovations, you can ensure a competitive edge in an increasingly digital world.
Manufacturing resource planning in practice
Incorporating manufacturing resource planning (MRP) into your operations involves merging operational technology with IT systems and using real-time data for better decision-making. The process also enhances supply chain integration, improving efficiency and productivity.
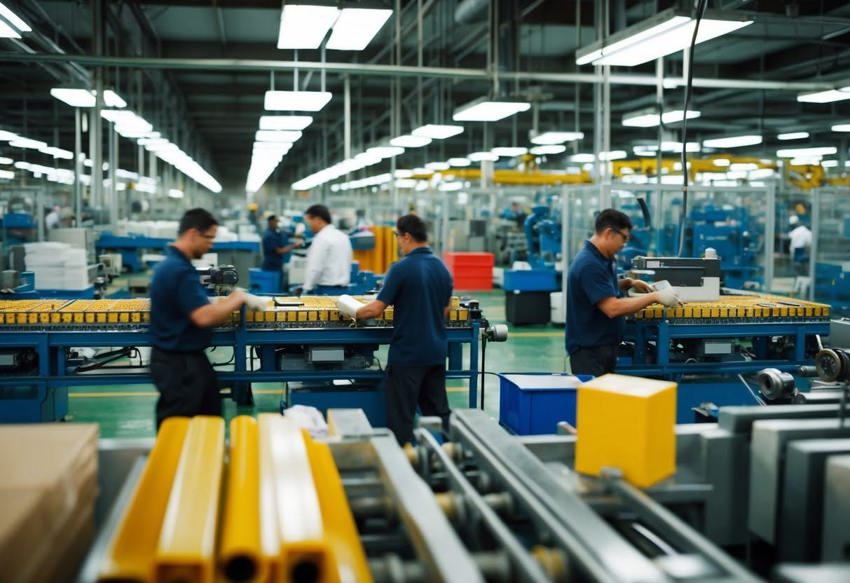
The marriage of operational technology and IT
Connecting your operational technology with IT systems enables seamless communication across production facilities. This alignment improves visibility into the manufacturing process for smoother operations. It also allows you to automate tasks, reducing errors and enhancing productivity.
Key tools used in this integration include sensors and IoT devices, which provide valuable data. This data helps you monitor equipment performance and optimise maintenance schedules. IT systems, like ERP software, manage and analyse this data, providing a single source of truth and actionable insights for better planning.
Efficient integration supports a more responsive and flexible manufacturing environment. It aids in quick adaptation to changes, meeting customer demands effectively.
Real-time data for informed decisions
Utilising real-time data helps you make informed decisions in MRP. This data gives you an accurate picture of your current operations, tracking inventory levels, managing production schedules and forecasting demand accurately. Real-time monitoring helps you identify bottlenecks or delays, allowing you to address them quickly.
Accessing up-to-date information supports efficient resource allocation. It also helps reduce waste, ensuring you're using materials and labour efficiently and effectively. By leveraging up-to-date data, you can improve your overall efficiency and maintain a competitive edge.
Integrating the supply chain
Effective MRP requires tight integration of your supply chain. You need a clear view from suppliers to the end customer. This full view enhances communication and planning across all stages of production. It ensures better coordination in material procurement, reducing the risk of shortages or excesses.
Supply chain management (SCM) tools are also useful. They help track shipments, monitor supplier performance and optimise logistics. Aligning these with your MRP system ensures you meet production targets efficiently. This comprehensive view reduces lead times and improves customer satisfaction. These features are all available as part of Dynamics 365, which offers many manufacturing-specific modules to help you manage and optimise your operations.
A well-integrated supply chain supports adaptive strategies, helping you navigate market changes with confidence.
The influence of advanced technologies
Advanced technologies are reshaping manufacturing by improving efficiency, precision, and overall productivity. From understanding data through machine learning to leveraging the expansive capabilities of cloud computing and the impact of additive manufacturing, these technologies are integral parts of modern manufacturing processes.
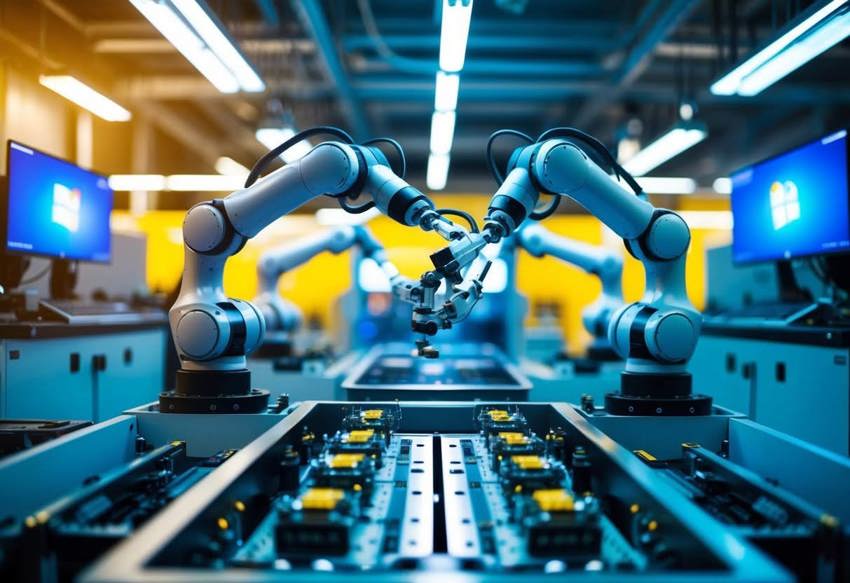
Machine learning and predictive analytics
Machine learning is transforming how you manage resources in manufacturing. By analysing vast amounts of data, it predicts maintenance needs, reduces downtime and optimises inventory. Predictive analytics, a powerful feature of machine learning, helps you anticipate demand changes and streamline supply chains.
These features lead to more informed decision-making and improved operational efficiency. Integrating machine learning into manufacturing enhances automation, enabling smarter, more responsive systems that can adapt to real-time changes, significantly boosting competitiveness in the market.
Cloud computing and its capabilities
Cloud computing offers unparalleled capabilities, enabling you to access and store data more efficiently. With real-time data analytics and seamless connectivity, you can easily manage large-scale operations. The cloud provides flexibility, allowing you to scale resources based on demand.
Additionally, cloud solutions enhance collaboration by providing a centralised platform for data access. This means you can reduce IT infrastructure costs and increase your operation's flexibility and resilience. The use of cloud technology supports autonomous robots and smart machines, integrating them seamlessly into your processes.
Additive manufacturing: a paradigm shift
Additive manufacturing, also known as 3D printing, allows you to create complex parts with precision and minimal waste. Its ability to produce customised items quickly means you can bring products to market faster. Additive manufacturing supports design flexibility, enabling you to innovate without traditional manufacturing constraints.
By adopting this technology, you reduce material costs and improve product design processes. Incorporating additive manufacturing into operations ensures you stay at the forefront of industry advancements and remain competitive in a crowded market.
Challenges and considerations for adoption
Adopting manufacturing resource planning (MRP) involves key challenges like ensuring security in a digital environment, investing in skills and understanding how to measure return on investment (ROI) and performance impacts.
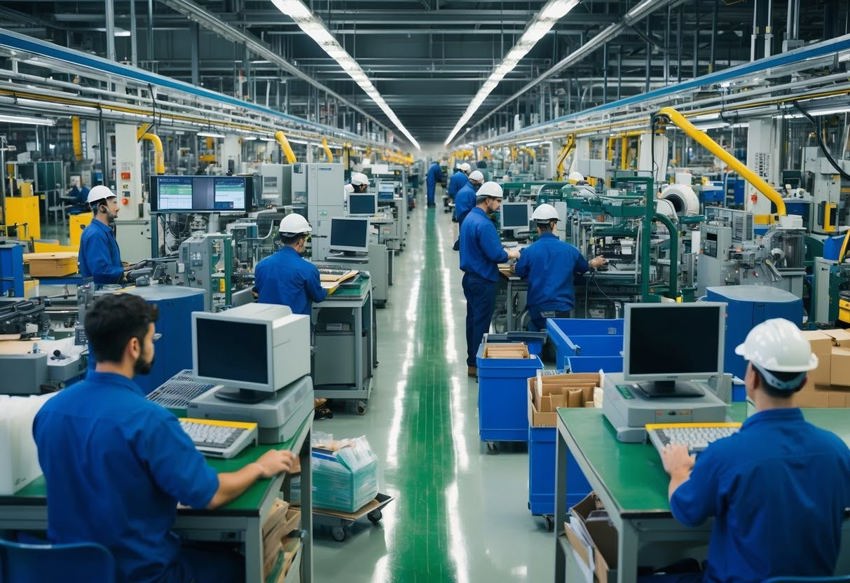
Security in a digitally connected environment
Digitally connected systems, from back-office software to manufacturing machinery, can be vulnerable to malicious attacks. You should regularly update security protocols to protect sensitive data. Implementing firewalls and encryption can prevent unauthorised access and protect the integrity of factory floor operations.
Additionally, training your staff in cybersecurity practices is essential. Employees must be able to recognise phishing attempts and other potential threats. Assess your current security measures and look for areas of improvement, as this will help you safeguard your investment and maintain operational efficiency.
Investment in skills
To fully benefit from MRP, you should invest in both skills and infrastructure. Smart manufacturing and resource planning tools often require upskilling your workforce.
Employees should be familiar with both the software and the principles of MRP. Consider hosting workshops or training sessions to build these skills. Investing in talent and technology ensures that you stay competitive and that your systems run efficiently and smoothly.
Measuring ROI and performance impact
Understanding the performance impact and ROI of MRP allows you to assess its value to your business. You should establish clear metrics and benchmarks to evaluate improvements in production efficiency and cost savings. Regular performance assessments can highlight areas where MRP has enhanced operations, such as reduced waste or improved scheduling.
Consider developing a framework for ongoing evaluation. This should include financial metrics and soft benefits, like increased agility in responding to market changes. By tracking these indicators, you can determine if your MRP investment is achieving its goals and make informed decisions about future investments.
Frequently asked questions
Manufacturing resource planning helps create efficient manufacturing processes. Understanding its intricacies can greatly enhance your production strategies. This section addresses common questions to help clarify key points and processes involved.
How can manufacturing resource planning software streamline operations within a manufacturing environment?
MRP II software streamlines operations by offering tools for scheduling, inventory management, and capacity planning. It enables better resource allocation and real-time data access, which helps in reducing waste and improving productivity.
How do manufacturing resource planning systems offer advantages and what limitations should I be aware of?
MRP systems provide significant advantages like improved resource utilisation and reduced production waste. However, they also have limitations, such as requiring precise data inputs and possibly high initial setup costs.
What are the steps involved in implementing an MRP system within a manufacturing firm?
Implementing an MRP system involves several steps. First, assess current processes and define objectives. Next, select suitable software like Dynamics 365 and the modules your business needs. Then, train staff and finally, monitor and adjust the system as required to ensure success.
What are the latest trends and technological advancements influencing manufacturing resource planning today?
Current trends include the integration of AI and machine learning for predictive analytics, enhancing MRP II systems' ability to forecast demand and optimise resources. Cloud-based solutions are also gaining popularity, offering flexible access and scalability.
Jesse Lawrence
Jesse is our marketing manager, keeping an eye on the latest news in the market as well as having worked on the GDPR legislation.