Implementing the right ERP system for your business is an important step in digital transformation, which is gaining more traction in the manufacturing sector. Automating processes can help you save time and money, to truly digitally transform, you should be using technology for continuous improvement and staying ahead in a competitive market. Your chosen ERP should be scalable and flexible, supporting you as your business evolves.
Implementing an ERP system requires careful planning. Engage your team in the process, from selection to deployment, to ensure seamless integration and adoption. This approach will empower your workforce, ensuring long-term success and satisfaction.
Key takeaways
- The right ERP software enhances business growth.
- Look for core features that match your needs.
- Successful implementation depends on team involvement.
Understanding ERP systems in manufacturing
Implementing ERP systems in the manufacturing industry addresses challenges including operational efficiency and data management. These systems provide a modern solution by offering functionalities that streamline production, supply chain and business operations.
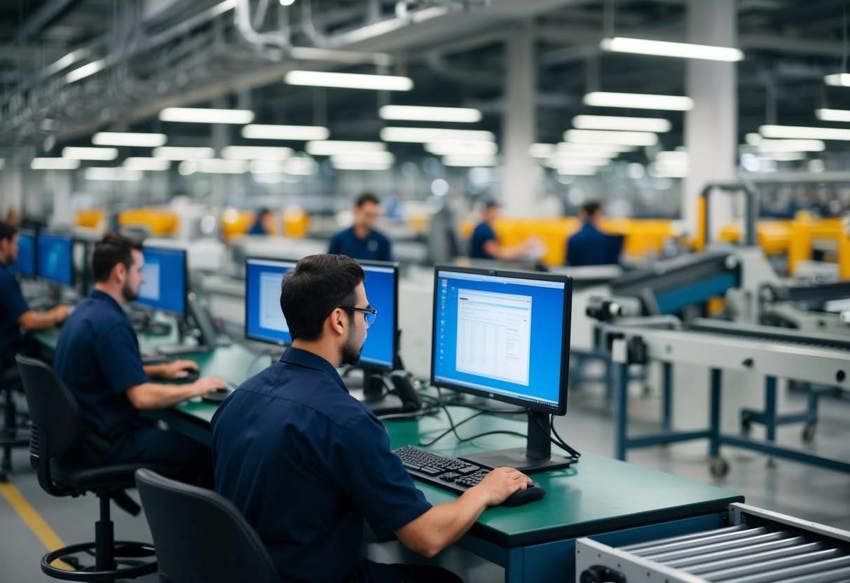
The role of manufacturing ERP
Manufacturing ERP systems play a central role in coordinating various business activities. They integrate production schedules, inventory management and order processing, allowing you to manage your business' entire operations through one solution. With ERP, you can monitor production in real time, reducing inefficiencies and enhancing responsiveness. At a time when manufacturers are facing unpredictable market demands, this ability to react to market changes is invaluable. ERPs offer insights that support decision-making, so you can maintain a competitive edge in the market.
Evolution from legacy systems to modern solutions
Transitioning from legacy systems to modern ERP solutions has transformed manufacturing processes. Legacy systems often lack the flexibility and adaptability of contemporary ERP software. Modern solutions, particularly cloud-based ERP solutions like Dynamics 365 Business Central, provide scalability and accessibility.
These advancements reduce IT costs and improve system updates. By adopting integrated solutions, manufacturing firms are not only enhancing productivity but are also positioned to address complex manufacturing challenges. This level of adaptability is important in a market dealing with an uncertain global economy.
Key functionalities and advantages for manufacturing
Leading Manufacturing ERP systems come with a suite of functionalities that are tailored to the sector's unique needs. Key features include comprehensive inventory management, production planning, quality control and supply chain management.
Systems like Dynamics 365 Business Central automate routine tasks, minimising errors and labour costs. With enhanced data analytics tools and a real-time overview of your operations, you can track performance metrics and optimise manufacturing operations. These advantages contribute to improved efficiency and reduced operational costs, which are essential for gaining and retaining a good market share. Enhanced reporting and data accuracy, with a single version of the truth, also empower manufacturers to make informed decisions.
Core features to look for in manufacturing ERP software
When selecting manufacturing ERP software, you need to consider features that enhance efficiency and streamline operations. These include robust support for inventory control and production management, as well as customer-focused services. These features ensure your business remains competitive and compliant.
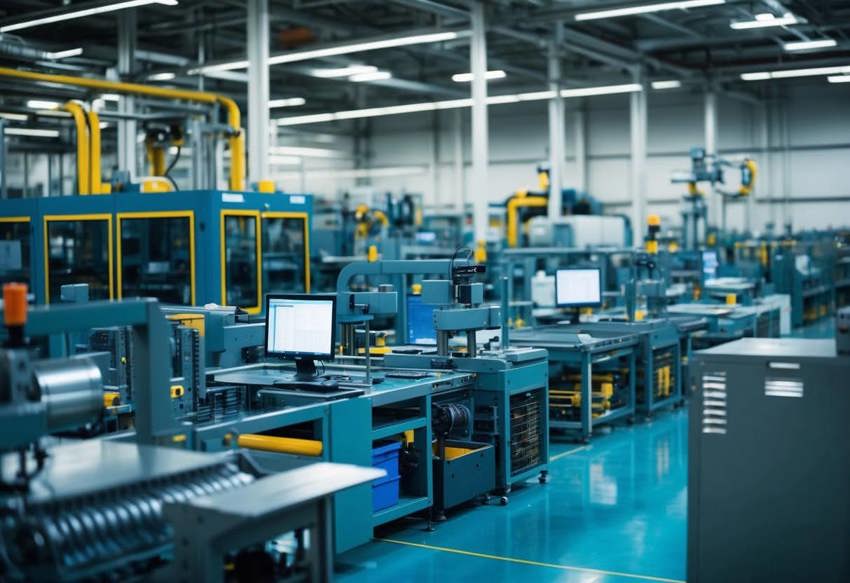
Inventory and supply chain management
Effective inventory management helps you maintain a balance between continually shifting supply and demand. Your ERP software should offer real-time visibility into inventory levels, helping you to manage stock efficiently. Look for features that include automated reordering, detailed item tracking and integration with supply chain operations.
A strong supply chain management component helps you coordinate with suppliers and distributors. This helps you ensure the timely delivery of materials and products, ultimately improving production schedules and reducing costs. By optimising these processes, you can minimise waste and enhance productivity.
Production scheduling and control
Production scheduling helps you meet customer demands promptly. Your ERP solution should support detailed production planning, including task scheduling and resource allocation. This ensures that all resources are used effectively, reducing downtime and increasing output.
Control mechanisms within the ERP can help track progress and address any bottlenecks. This includes monitoring production lines in real-time and adjusting schedules as needed. By having a comprehensive overview of the production process, you can make informed decisions quickly, helping maintain efficiency and quality.
Quality management and regulatory compliance
Your ERP software should include quality management tools for monitoring quality at each production stage. This helps in identifying defects early and maintaining consistent product quality. In turn, this can help improve customer satisfaction.
Regulatory compliance features are essential for adhering to industry standards and legal requirements. Your manufacturing ERP software should assist with documentation, process checks and audits to ensure full compliance. This not only helps avoid legal issues but also builds trust with your customers.
Customer relationship management and order processing
An ERP with customer relationship management (CRM) capabilities helps manage customer data, track interactions and analyse purchasing trends. This allows you to personalise communications and improve customer satisfaction.
Efficient order fulfilment within the ERP ensures that customer orders are handled smoothly and promptly. The system should track orders from placement to delivery, ensuring accuracy and timely fulfilment. By improving these processes, you can enhance customer experience and loyalty.
Selecting the right manufacturing ERP solution
To choose the right ERP solution for manufacturing, you need to consider the features available, your deployment method, system compatibility, associated costs and future scalability. Getting these elements right means your manufacturing ERP software will support your operations and business growth effectively.
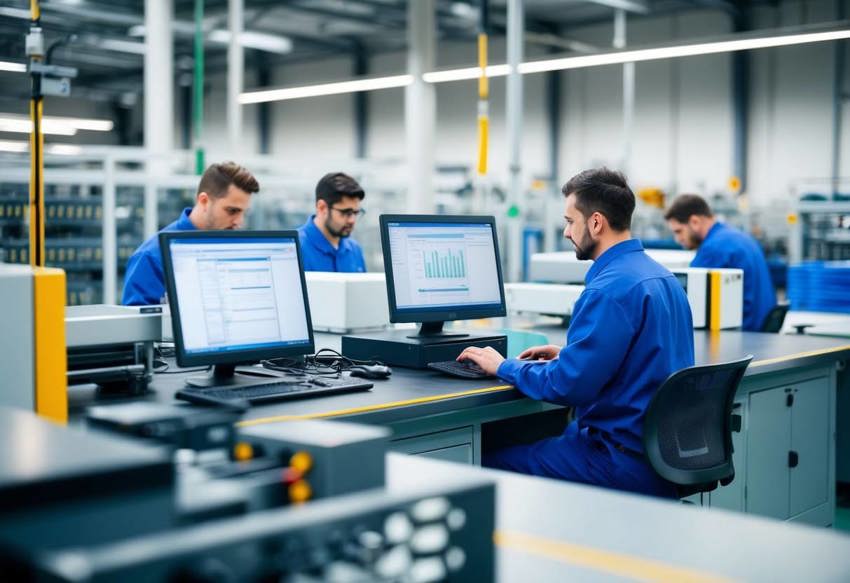
Comparing cloud vs on-premise systems
When deciding between cloud ERP and on-premise ERP systems, consider your business needs and infrastructure. Cloud ERP offers flexibility, scalability, access from anywhere and robust security features. It eliminates the need for in-house infrastructure and a large upfront cost. Updates are automatic, keeping your system current without extra effort.
On-premise systems may offer more control over data and customisation. However, they require a lot of space on-premise to run, which can become costly, and are harder to upgrade or integrate with other software. Evaluating these factors helps determine the best fit for your company’s operations and budget, ensuring smooth business processes and improved efficiency.
Assessing compatibility with business processes
Your ERP system needs to align with your business processes - and in fact, ERP systems like Dynamics 365 Business Central can help streamline or automate some of them. Start by documenting your existing workflows, identifying gaps or inefficiencies that a new system could address. The ERP should support your specific business model, whether it's discrete, process, or engineer-to-order manufacturing.
You should review systems that have features tailored to your industry. Look into features like inventory management, procurement and financial management, all of which comes as standard in Dynamics 365 Business Central. Check if the system integrates seamlessly with your existing software. Assessing user-friendliness to ensure easy adoption by your team, reducing the learning curve and minimising disruptions during transition.
Understanding costs: from implementation to ongoing
Implementation fees can vary based on system complexity and customisation needs. Generally, a cloud implementation will be cheaper than on-premise, and it'll also come without an upfront purchase fee. It's wise to factor in training and data migration costs during the initial phase too. Once your ERP is in place, calculate ongoing costs like subscription fees for cloud systems or maintenance fees for on-premise solutions.
Evaluating how costs align with overall business benefits and return on investment can help you assess if your ERP system is working for your business once implemented. Selecting an ERP that meets budget constraints without compromising on functionality ensures better financial management and resource allocation for your business.
Ensuring scalability and support for business evolution
As your business evolves, your ERP system should grow with you. Evaluate your solution’s scalability by checking how well it can handle an increase in data, users and transactions. Scalable systems support business expansion without significant downtime or costly overhauls.
Additionally, assess the provider’s support services, or external providers like our Business Central support services. Reliable support is important during growth phases, ensuring minimal disruption. Look for flexibility in adding functionalities and upgrading the system as your business requirements change. Choosing an ERP that supports future needs helps sustain smooth operations and maintains competitive advantage over time.
Leveraging your ERP for continuous improvement
Manufacturing ERP software can help your business evolve and grow. It does this by using real-time insights and integrating new technologies. With these tools, you can gain a competitive edge and make informed decisions.
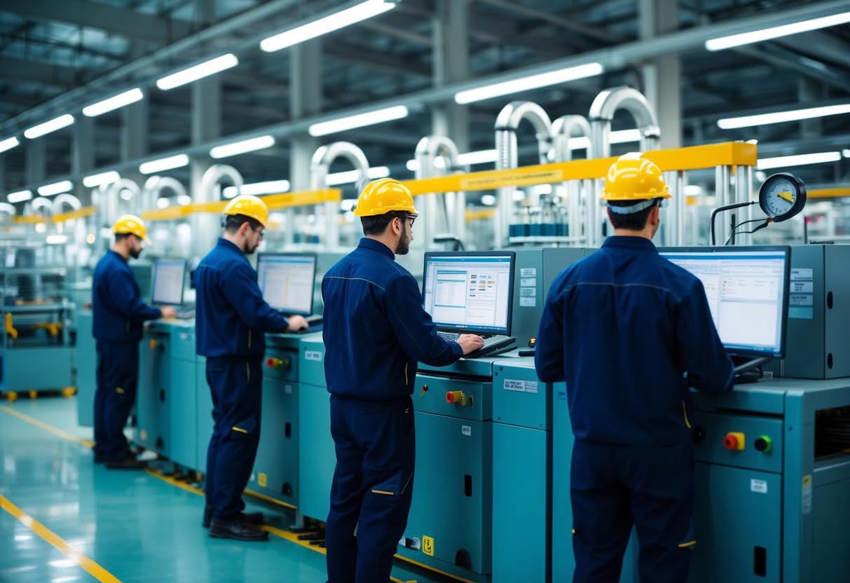
Gathering insights with business intelligence
Using ERP software, you can gather detailed business intelligence. This involves collecting real-time data across production, sales and supply chain. These insights support informed decisions, allowing you to spot trends and improve operations.
Analytics tools within your ERP can identify areas for cost-saving and boosting productivity, and AI-driven business intelligence can predict future demands, helping you stay ahead. Data visualisation tools like Power BI make it easier to understand complex information quickly. This gives your business a clear advantage in a fast-paced market.
Integrated technologies and innovations
Automation tools within your ERP can streamline processes, reducing manual work and errors. This increases efficiency and frees up time for your team.
Cutting-edge innovations, such as the Industrial Internet of Things (IIoT), can further enhance your ERP capabilities. Connecting devices and systems provides a more seamless operation. Integrating machine learning can also offer deeper insights into production and maintenance needs.
By adopting these technologies, your business becomes more agile and ready to tackle new challenges. Embracing innovation ensures you can adapt and thrive in an ever-changing industry landscape.
Frequently asked questions
What key factors should be considered when selecting an ERP system for a manufacturing enterprise?
When choosing an ERP system for manufacturing, you should focus on scalability, ease of integration and industry-specific features. Ensure the software can handle your production processes and supports future growth needs effectively.
How does an ERP solution enhance efficiency within a manufacturing business?
An ERP solution streamlines operations by integrating processes like production planning, inventory management and distribution. This integration leads to improved communication and coordination across departments, accelerating decision-making and reducing delays. ERP systems also help in tracking performance and identifying bottlenecks.
What benefits should small to medium-sized manufacturing firms expect from an ERP software?
Small to medium-sized businesses can benefit from ERP software by gaining better control over their production and finances. Systems like Dynamics 365 Business Central offer comprehensive tools for managing resources efficiently, leading to increased productivity and profitability. Firms can also achieve improved compliance and reporting.
In what ways can ERP software improve productivity and cost-management for manufacturers?
ERP software enhances productivity by automating manual tasks and offering real-time visibility into performance and business processes. It helps in reducing operational costs through efficient resource allocation and inventory management. By having a real-time overview, manufacturers can make informed decisions that optimise resource use and lower waste.
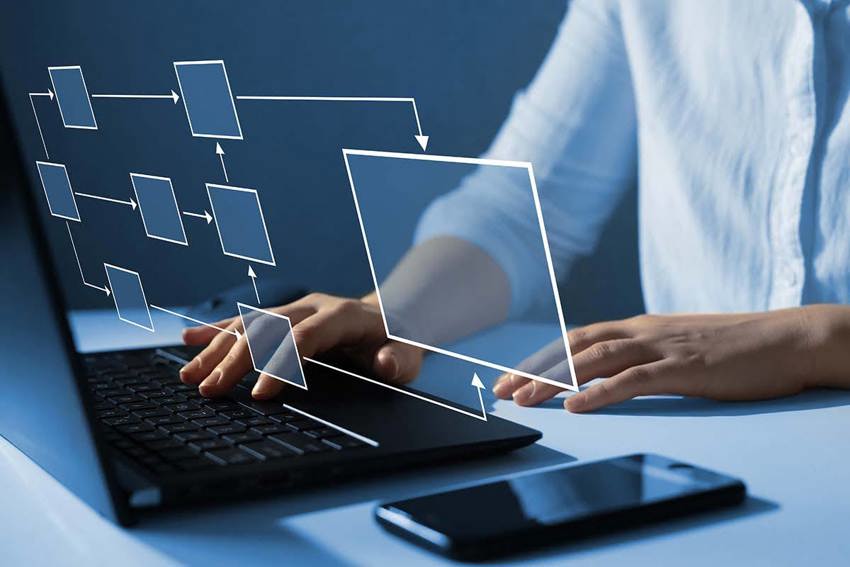
What criteria define the top ERP systems for manufacturing operations?
Top ERP systems for manufacturing are defined by their ability to provide comprehensive support for end-to-end manufacturing management. Features to look for include robust production planning, inventory control and customer relationship management. Dynamics 365 Business Central is recognised for its powerful sector-specific features, adaptability, scalability and user-friendly interfaces.
Could you explain the advantages of integrating a manufacturing-specific ERP rather than a generic ERP system?
Manufacturing-specific ERP systems are tailored to address the unique challenges within the industry. They offer specialised features such as batch tracking and quality control that generic ERPs might lack. A tailored ERP solution ensures better alignment with your business processes, resulting in more efficient operations and competitive advantage.
Jesse Lawrence
Jesse is our marketing manager, keeping an eye on the latest news in the market as well as having worked on the GDPR legislation.