The convergence of IT and operational technology creates a seamless production environment that manufacturers can use for real-time data analysis and decision-making. With tools like industrial IoT and robotics, businesses are not just automating tasks but also creating an interconnected landscape of efficiency.
Exploring industry 4.0 further opens doors to understanding its core components, like artificial intelligence and big data analytics. Embracing these technologies can position your company at the forefront of innovation, UK manufacturing’s core strength, enabling you to overcome challenges and adapt to future trends.
Key takeaways
- Industry 4.0 boosts efficiency with interconnected digital technologies.
- Core components include IoT, AI and robotics in manufacturing.
- Adoption enables real-time decision-making and competitive advantage.
Core components of industry 4.0
Industry 4.0 transforms manufacturing by integrating advanced technologies that elevate efficiency and innovation. These components drive automation, connectivity and smarter operations within manufacturing.
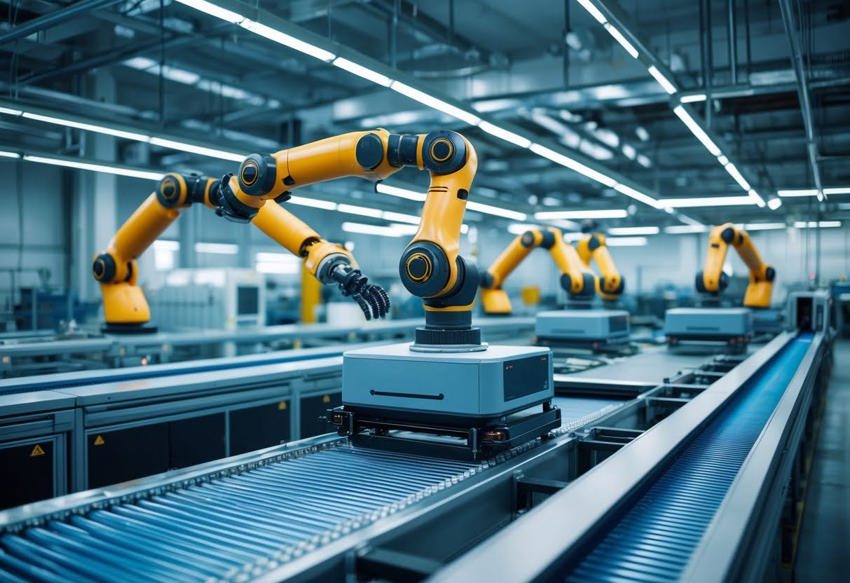
Cyber-physical systems and smart factories
Cyber-physical systems are central to smart factories. These systems integrate computing capabilities with physical processes, allowing machines to interact and make decisions with minimal human interference. In a smart factory, machines equipped with sensors collect and share data across networks to optimise operations.
This environment fosters smart manufacturing, where self-aware systems enhance production efficiency and reduce downtime. By automating routine tasks, you can focus on more complex decision-making, increasing competitiveness through flexibility and responsiveness to market demands.
Cloud computing and big data analytics
Cloud computing supports industry 4.0 by providing efficient data storage and processing solutions. Through a cloud environment, manufacturers manage large volumes of data generated by factory operations. This approach ensures that data is accessible, scalable and secure.
Big data analytics processes this vast amount of information to uncover insights that drive improvements. Using analytics, you can optimise your supply chains, predict equipment failures, and enhance product quality. Using cloud-based data management platforms like Dynamics 365 enables collaboration across multiple sites and departments, contributing to seamless operations.
The internet of things (IoT) and connectivity
IoT involves connecting devices and systems to the internet, enabling them to communicate and share data. In manufacturing, IoT devices collect real-time information from production lines, offering insights that guide decision-making.
Connectivity through IoT allows for the remote monitoring and management of processes, reducing the need for on-site presence. This connectivity enhances transparency across the supply chain and improves response times to unexpected events. Implementing IoT helps you maintain a competitive edge by maximising operational efficiency and reducing costs.
Autonomous robots and additive manufacturing
Autonomous robots play a critical role in industry 4.0, performing tasks without human intervention. These robots are integrated with sensors and machine learning algorithms, enabling precise, efficient operations. They handle repetitive tasks, improve safety and increase productivity.
Additive manufacturing, or 3D printing, transforms production by allowing on-demand creation of parts and products. This technology reduces material waste and cuts down lead times, offering customisation at lower costs. Integrating autonomous systems with additive manufacturing enables you to innovate rapidly and meet complex manufacturing needs efficiently.
Driving efficiency in the manufacturing process
Industry 4.0 technologies boost manufacturing efficiency with real-time data and advanced analytics. They ensure higher product quality and streamlined supply chain management. These technologies also improve asset utilisation and operational efficiency.
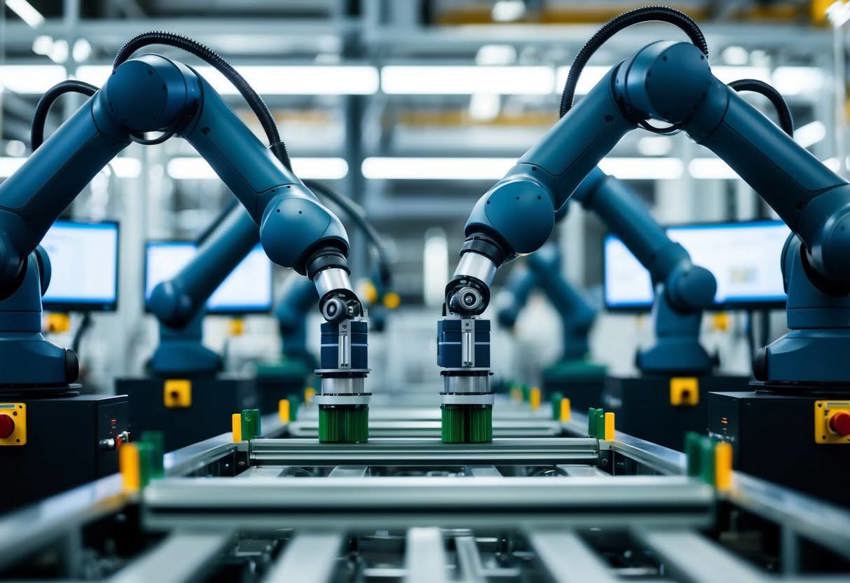
Enhancing product quality
To improve product quality, industry 4.0 integrates smart systems on the factory floor. Sensors continuously monitor the production process, instantly identifying defects and enabling quick corrections. This reduces waste and improves consistency in mass production.
Smart machinery and cyber-physical systems play a central role. They allow you to adjust parameters in real time, ensuring each product meets quality standards. Predictive maintenance also minimises downtime, ensuring machines operate at optimal capacity and further enhancing product quality.
Optimising supply chain management
Effective supply chain management relies heavily on integrating technology to manage production schedules and materials. By adopting industry 4.0 tools, you gain real-time insights into supply chain operations, enabling more accurate demand forecasts and stock management.
Technologies such as the internet of things (IoT) and cloud computing help track assets and optimise logistics. This results in better asset utilisation, reducing costs and increasing delivery speed. Predictive analytics also shed light on potential disruptions, allowing for proactive supply chain adjustments.
Real-time data and predictive analytics
Real-time data and analytics allow you to optimise the manufacturing process. Sensors and connected devices on the factory floor collect vast amounts of data, offering insights into every aspect of production.
Implementing predictive analytics transforms this data into actionable insights. You can predict maintenance needs, reduce unexpected downtime and optimise operational efficiency. This ensures processes run smoothly and increases the longevity of machinery. Enhanced data-driven decision-making improves response times and supports you in strategic planning.
Challenges and future outlook
Navigating the world of industry 4.0 involves several challenges and potential transformations. Key issues include integrating cutting-edge technologies, ensuring data security and adapting to new business realities.
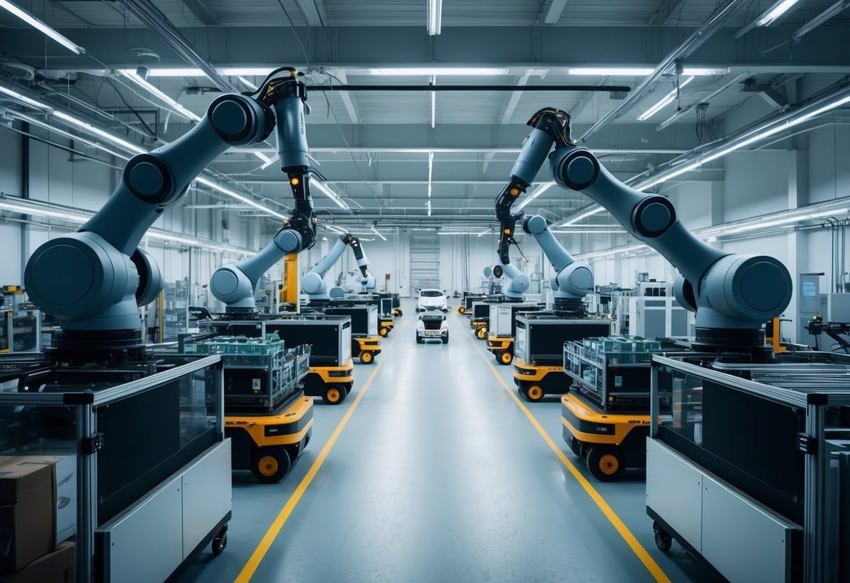
Integrating advanced technologies
The integration of smart technologies and digital tools is central to Industry 4.0. While offering significant operational benefits, these technologies of industry 4.0 often come with challenges. As businesses integrate systems such as artificial intelligence and Internet of Things (IoT), they must plan for staff training.
Organisations should also ensure seamless communication between digital and operational technology. Creating a cohesive strategy will enhance efficiency and productivity. Despite these hurdles, investing in the right technology can help transform your manufacturing operations for the better.
Ensuring data security and privacy
With the rise of industry 4.0, safeguarding data has become crucial. The increasing interconnectivity of devices heightens the risk of malicious attacks. This means robust cybersecurity measures must be a priority. Companies need to employ advanced monitoring systems to detect and prevent unauthorised access.
Implementing strong encryption and using secure networks can protect sensitive information. Educating employees about data privacy and implementing regular security audits is equally important. Tools like Microsoft Dynamics 365 come with some of the most rigorous security protocols around, so it's wise to implement solutions wrapped in enterprise-grade security. Protecting your data will not only ensure compliance with legal standards but also boost customer trust and confidence.
Preparing for the future
Digital transformation is now a key business priority in manufacturing, with many firms accelerating their adoption of new technologies to stay competitive. Your readiness to embrace digital solutions will determine how effectively you adapt and thrive in the evolving market. Engaging with partners who understand the future of industry will help you meet the demands of a post-pandemic world.
Frequently asked questions
Industry 4.0 has transformed the manufacturing landscape by integrating advanced technologies like IoT, AI and cloud computing.
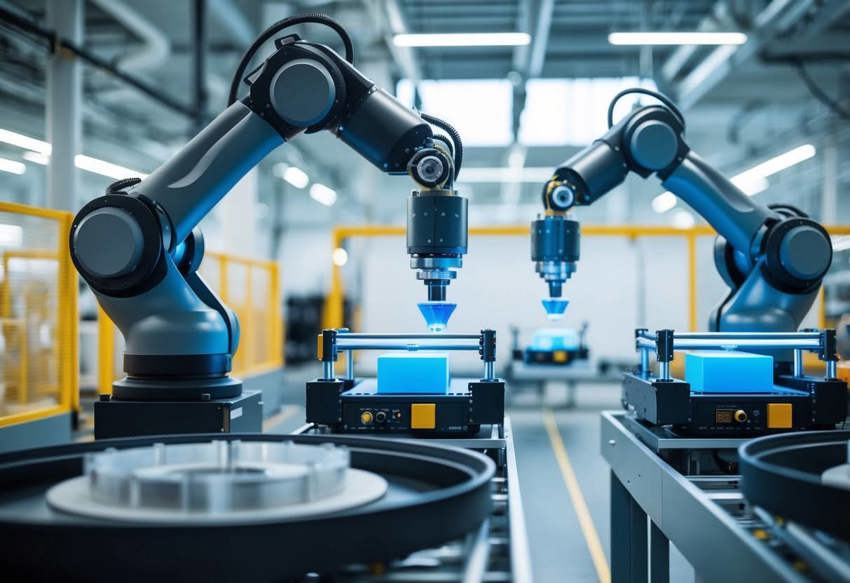
What are the essential components of industry 4.0 in the manufacturing sector?
Industry 4.0 involves several key technologies including cloud computing, IoT, AI and machine learning. These components work together to enhance production efficiency. Digital technologies are integrated into manufacturing processes, creating smarter systems.
How can manufacturers effectively strategise for the integration of industry 4.0?
To effectively strategise for Industry 4.0, manufacturers need to audit their existing systems. It's important to understand the current capabilities before introducing new technologies. Starting with an analysis of processes and assets can help identify areas for improvement.
What steps are involved in the successful implementation of industry 4.0 technologies?
Successful implementation begins with laying a solid foundation for new technologies. This includes preparing existing systems and ensuring minimal disruptions during integration. Manufacturers should focus on gradual integration to allow these technologies to enhance processes efficiently.
Could you explain some of the common terminology used in industry 4.0?
Industry 4.0 uses specific terminology that includes concepts like cyber-physical systems (CPS), IoT and smart manufacturing. These terms help us describe the technologies and methods driving this industrial revolution.
Which software solutions are pivotal for industry 4.0 adoption in manufacturing?
Key software solutions for industry 4.0 adoption include cloud storage and real-time data processing applications. These tools help in facilitating smart manufacturing and improving process efficiency. Data-driven software plays a vital role in managing and analysing complex manufacturing data.
How has the timeline of industry 4.0’s evolution affected its adoption in 2024?
The rapid evolution of Industry 4.0 has significantly increased its adoption in 2024. As technologies such as AI and IoT become more advanced, more companies are investing in these innovations to stay competitive. The ongoing developments have made these technologies more accessible and practical for widespread use.
Jesse Lawrence
Jesse is our marketing manager, keeping an eye on the latest news in the market as well as having worked on the GDPR legislation.