Understanding the essentials of a production schedule involves grasping key factors such as production capacity and resource allocation. By integrating technology into your scheduling process, you can gain insights that help refine your operations and stay competitive.
Implementing a production schedule is not a one-time task but an ongoing process that benefits from continual improvement. Contingency planning is an important element that helps you adapt to unexpected changes, ensuring minimal disruption. Addressing these aspects can lead to a robust schedule that supports your long-term business goals.
Key takeaways
- Effective planning boosts production efficiency.
- Use technology to enhance scheduling processes.
- Continual improvement is key to robust scheduling.
Understanding the essentials of production scheduling
A well-crafted production schedule is essential for efficient manufacturing operations. It balances resource availability, capacity constraints and customer demand to optimise production processes and meet business goals.
Defining production schedules and their importance
Production schedules are detailed plans that outline the workflow of tasks and timelines in a manufacturing process. They set the sequence of activities to ensure that products are produced on time. A clear production schedule helps to minimise downtime, streamline operations and enhance productivity.
Understanding their importance can significantly impact a company’s efficiency and profitability. By having a structured schedule, you can allocate resources better, prevent bottlenecks and improve time management. It's especially useful in complex manufacturing environments where multiple tasks and processes need to be coordinated effectively.
Assessing resource availability and capacity constraints
Evaluating resource availability involves checking the stock of materials, equipment and labour required for production tasks. Understanding these elements helps you create an accurate manufacturing schedule. By knowing what resources you have, you can avoid delays that might occur due to shortages.
Capacity constraint refers to the maximum throughput your production line can handle. Planning within these limits ensures that you don’t overpromise to customers and can maintain a smooth production flow. This practice helps identify potential issues beforehand and planning for maintenance or adjustments as necessary.
Integrating production schedule with customer demand
Aligning your production schedule with customer demand helps you maintain and even improve customer satisfaction. A master production schedule is a useful tool, as it summarises production tasks, timelines and the quantity of items needed. By integrating demand forecasts, you ensure that the right products are produced at the right time.
This integration helps reduce lead times and inventory costs by preventing overproduction or underproduction. It also allows you to quickly respond to market changes, adapting your schedule accordingly. This proactive approach can boost your responsiveness and maintain competitiveness in the market, thereby strengthening your relationship with customers.
Designing an effective production schedule
Creating an effective production schedule helps manufacturers optimise processes and meet customer demands. By understanding market trends, efficiently allocating resources and ensuring timely delivery, you can enhance manufacturing results and customer satisfaction.
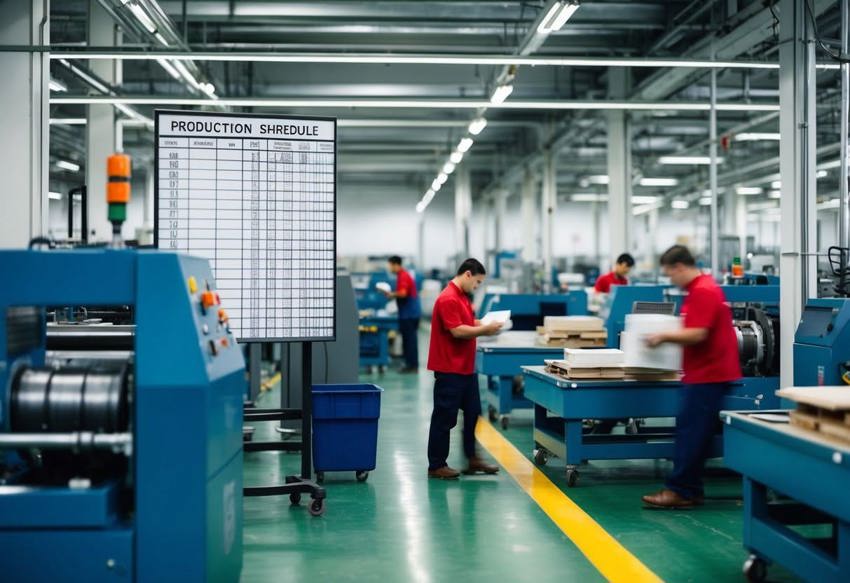
Incorporating market trends and future demands
To design an effective production schedule, keep a keen eye on market trends. Understanding the current market helps you anticipate future demands, ensuring that your products align with customer expectations. Demand forecasting allows you to adjust production schedules based on anticipated changes in consumer habits or industry shifts.
Utilising tools like Dynamics 365 Business Central for demand forecasting can provide valuable insights. Regularly anal this data to guide your production decisions, preventing overproduction or underproduction. By doing so, you're better equipped to maintain efficiency and address customer needs effectively.
Resource allocation for maximum efficiency
Optimal resource allocation is a cornerstone of effective production scheduling. You should focus on identifying and utilising available resources, such as manpower, machinery and materials, to their fullest potential. Proper resource allocation ensures that production processes operate smoothly without unnecessary delays.
Tools like Dynamics 365 contain built-in resource management modules to streamline this process. These tools can help you monitor resource utilisation and identify bottlenecks, enabling you to adjust allocations swiftly. By maintaining a balance between available resources and production needs, you can achieve maximum efficiency and reduce costs.
Timely delivery: balancing production time and customer satisfaction
Timely delivery is essential for customer satisfaction in manufacturing. Balancing production time with delivery schedules ensures that products reach customers when expected, enhancing trust and reliability. Effective production scheduling must incorporate strategies to minimise delays and streamline operations.
Focus on setting realistic production timelines that consider potential disruptions and incorporate contingency plans. Regular communication with suppliers and logistic partners can help you overcome unforeseen challenges. By prioritising timely delivery, you not only meet customer expectations but also build a reputation for reliability, creating long-term client relationships.
Using technology for enhanced scheduling
Integrating technology into production scheduling can greatly enhance efficiency and flexibility. It involves using software like Dynamics 365 to manage tasks, utilising real-time data for informed decision-making and adopting dynamic scheduling methods to remain flexible and responsive.
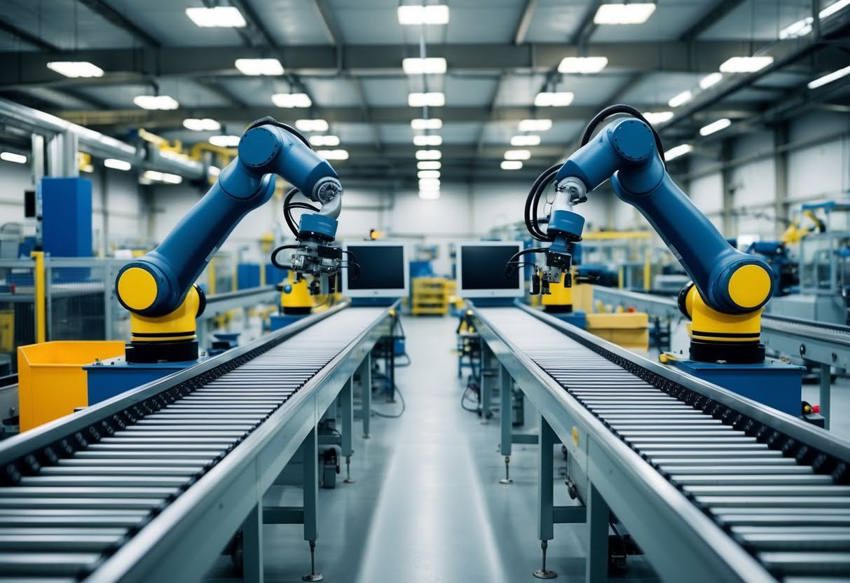
Production scheduling software features and advantages
Production scheduling software can transform how you manage your operations. Dynamics 365 Business Central includes production scheduling features including automated scheduling, capacity planning and sequencing, all powered by advanced algorithms. With these tools, you can optimise resource utilisation while minimising downtime.
Additionally, Dynamics 365 includes dashboards that provide insights into production status, allowing you to adjust plans instantly. It allows for effective communication across your team through shared access to updated schedules, ensuring everyone stays informed and aligned on tasks.
Real-time data and its impact on production planning
Utilising real-time data in your production planning means you can adapt quickly to changes such as shifts in demand or unexpected disruptions. By continuously feeding data into your scheduling systems, you maintain an up-to-date view of your operations, which is essential for making quick, informed decisions.
Real-time data also supports advanced planning by providing deeper insights into trends and patterns. This approach ensures that your plans are always aligned with current market conditions and operational realities, reducing the risk of overproduction or inventory shortages.
Maintaining flexibility with dynamic scheduling methods
Dynamic scheduling methods equip your business to respond swiftly to changes without major disruptions. By incorporating algorithms and real-time data, dynamic scheduling allows for adjustments on the fly, ensuring optimal output even as variables change.
With dynamic planning, your production process remains agile, enabling you to adapt resources and timelines as needed. This flexibility not only improves efficiency but also helps maintain competitiveness in a rapidly changing industry landscape.
Continual improvement and contingency planning
Manufacturing relies on both improving processes and preparing for unexpected events. To ensure efficiency and reliability, production managers must focus on streamlining operations and developing strong contingency plans.
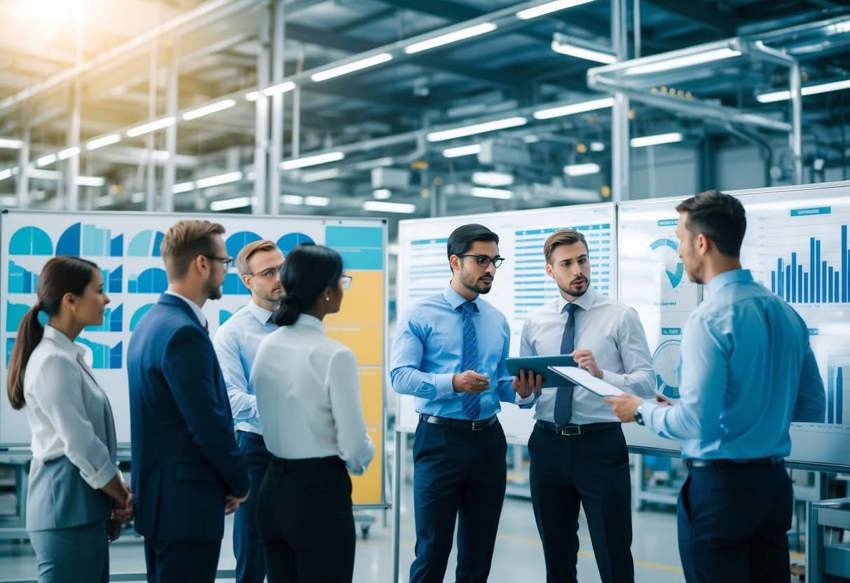
Assessing production processes for optimal flow
Continuous improvement in manufacturing involves assessing your production processes to identify areas needing enhancement. A thorough analysis can uncover inefficiencies such as wasted resources or bottlenecks. Production managers often use tools like value stream mapping to visualise the workflow and spot delays.
Engaging team members helps you understand issues from different perspectives. Regular feedback from the team encourages innovation and improvement. Adopting lean techniques can streamline processes, making them more efficient and reducing costs. These actions create a smoother production scheduling process that can respond quickly to changes in demand.
Developing contingency plans to manage unforeseen events
Creating contingency plans helps you handle unexpected disruptions. These plans act as backup strategies that keep the production line moving. Identifying potential risks, such as supplier delays or equipment failures, allows you to develop a comprehensive plan to tackle these issues.
Incorporating alternative suppliers or scheduling maintenance can prevent lengthy downtimes. Communicating these plans ensures that every team member knows their role during a disruption. Regularly updating contingency strategies is essential to adapt to changes in the business environment. This proactive approach helps maintain a steady workflow even during crises.
Measuring success with key performance indicators
To evaluate the effectiveness of improvements and contingency plans, you should use key performance indicators (KPIs). KPIs offer measurable insights into production efficiency, quality levels and response times to issues. These metrics are vital for assessing whether the implemented changes are meeting desired goals.
Common KPIs in manufacturing include cycle time, defect rates and on-time delivery rates. Analysing these indicators regularly provides clarity on the impact of your changes. When KPIs show positive trends, it indicates successful implementation, whereas negative trends highlight areas needing attention. This data-driven method ensures you can make informed decisions to further optimise production.
Frequently asked questions
When creating a production schedule, focusing on key elements like flexibility, integration with business processes and the use of technology can enhance efficiency. Considering these aspects helps to align production with market demands and adapt to changes smoothly.

What are the key components of an effective production schedule for manufacturers?
An effective production schedule includes demand forecasting, resource allocation and a master production schedule. The master production schedule offers a detailed timeline of products, their quantities and delivery timelines, ensuring operations run smoothly.
How do I incorporate flexibility into a production schedule to accommodate unexpected changes?
Incorporating flexibility involves allowing buffer times and maintaining extra capacity. This helps in managing unforeseen disruptions. Regularly updating and reviewing the schedule can also assist in adjusting to sudden changes in demand or supply.
What are the best practices for integrating production scheduling with other business processes?
Integration with inventory management, procurement and customer service ensures cohesive operations. Using tools that unify these processes, like Dynamics 365 and its dedicated modules, allows data sharing and streamlines your workflows, aligning production with overall business goals.
How can production scheduling software streamline manufacturing operations?
Production scheduling software can automate routine tasks, provide real-time data and enhance decision-making. By implementing this type of software or utilising modules in your existing Business Central subscription, manufacturers can ensure efficient production rates and timely deliveries, optimising workflow and reducing wastage.
How can small and medium-sized enterprises optimise their production schedules for efficiency?
SMEs can optimise schedules by focusing on accurate demand forecasting and resource management. Utilising basic scheduling tools and adopting lean manufacturing principles can result in cost savings and improved efficiency, tailoring operations to meet market needs.
What steps should a company take to effectively transition to a new production scheduling system?
Transitioning requires careful planning and employee training. Start with a pilot phase, gather feedback and adapt the system gradually. Ensuring all stakeholders are on board and understanding the benefits can facilitate a smoother switch to a new system.
Jesse Lawrence
Jesse is our marketing manager, keeping an eye on the latest news in the market as well as having worked on the GDPR legislation.